LARGE-SCALE
METAL FABRICATION
MACHINING and METAL SUPPLY
The Rose Corporation specializes in complex, large-scale industrial fabrication and contract manufacturing. Our team of highly-skilled metal fabricators and machinists have extensive experience building heavy industrial components and have a strong reputation for delivering the highest quality work on time and within budget.
LARGE-SCALE
METAL FABRICATION
MACHINING and METAL SUPPLY
The Rose Corporation specializes in complex, large-scale industrial fabrication and contract manufacturing. Our team of highly-skilled metal fabricators and machinists have extensive experience building heavy industrial components and have a strong reputation for delivering the highest quality work on time and within budget.
LARGE-SCALE INDUSTRIAL FABRICATION
Material handling systems, power generation equipment, structural steel components, and more.
MACHINING
Large-scale, high-precision machining services in the mid-Atlantic and East Coast regions.
WHOLESALE METAL SUPPLY
Mark Metals carries a wide “under-roof” inventory of stainless steel, aluminum, and carbon steel sheet, plate, bars, shapes, tubing, and pipe.
Why Choose ROSE?
Our passion is building large, complex industrial equipment. We consistently deliver exceptional value by applying our expert craftsmanship, experienced project management, and innovative solutions to our customers’ diverse manufacturing needs.
EXPERT CRAFTSMANSHIP
Since 1987, we have built a solid reputation for high-quality contract manufacturing, industrial fabrication, and installation of large-scale components and sub-assemblies.
EXPERIENCE
Our team includes highly skilled and experienced project managers, fitters, welders, machinists, and quality assurance personnel.
INNOVATIVE SOLUTIONS
We build what O.E.M. and engineering firms design and help them find real-world solutions to their industrial fabrication needs.
Request a Brochure
Download our company brochure which offers a more detailed look into The Rose Corporation’s fabrication and machining capabilities.
Testimonials
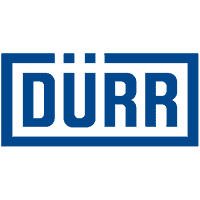
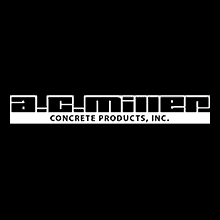
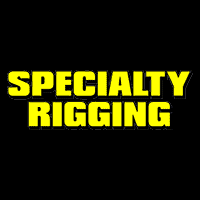
